Job Hazard Analysis: Improving Workplace Safety in High-Risk Industries
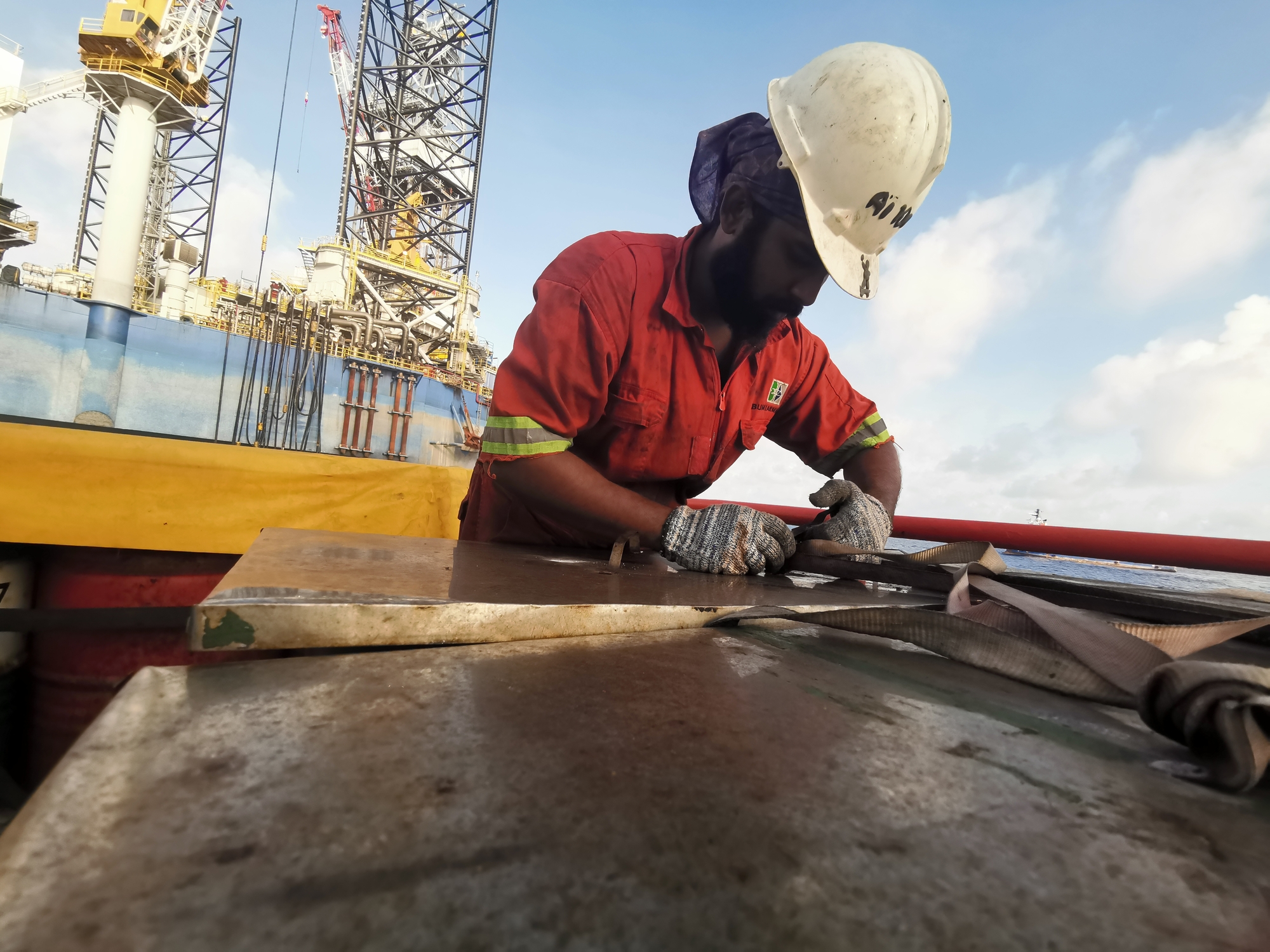
Industries like construction, mining, oil and gas, and manufacturing are essential to the global economy, but they come with high levels of risk. Workers in these fields face dangers ranging from heavy machinery accidents to chemical exposures. According to the International Labour Organization, over 374 million non-fatal workplace injuries occur each year, alongside 2.3 million work-related deaths. These sobering statistics underscore the critical need for proactive measures to protect employees. One of the most effective strategies for minimizing workplace hazards is Job Hazard Analysis (JHA). By systematically identifying and addressing risks associated with specific tasks, JHA helps companies reduce incidents, comply with safety regulations, and promote a culture of safety. This article delves into the importance of JHA, its implementation, and its potential for high-risk industries. To learn more about workplace safety services, visit Field1st’s Safety Consulting Services.
What Is Job Hazard Analysis?
Job Hazard Analysis, sometimes referred to as job safety analysis, is a process that examines workplace tasks to identify potential hazards and determine appropriate control measures. By focusing on individual tasks rather than broader safety policies, JHA provides a granular approach to risk management. This detailed methodology ensures that every step of a job is scrutinized for potential hazards and mitigated before work begins.
At its core, JHA involves breaking a task into smaller steps, analyzing the risks associated with each step, and developing strategies to eliminate or control those risks. For example, in a construction setting, a JHA might examine the process of erecting scaffolding. Each phase—assembling, climbing, and disassembling—would be reviewed to identify dangers such as falls, unstable platforms, or improper use of tools.
High-risk industries benefit significantly from JHA because they often involve complex tasks with inherent dangers. From handling toxic chemicals in manufacturing to maintaining equipment in oil refineries, JHA ensures that risks are addressed systematically, reducing the likelihood of accidents. Explore how Field1st’s Customized Risk Assessments can support your hazard analysis efforts.
Why Job Hazard Analysis Is Crucial in High-Risk Industries
Workplace safety programs often emphasize broad policies, but JHA drills down to the task level, ensuring no detail is overlooked. This makes it particularly valuable in high-risk sectors where the consequences of an oversight can be catastrophic. Here’s how JHA addresses key challenges in such industries:
1. Mitigating Safety Risks
Workers in high-risk industries face unique challenges that demand tailored safety measures. For instance, miners encounter risks like cave-ins, exposure to toxic gases, and equipment failures. Through JHA, supervisors can identify hazards for each task, such as operating drills or navigating confined spaces, and implement appropriate safeguards like ventilation systems or reinforced supports. To address these challenges, consider leveraging Field1st’s Safety Program Development.
2. Ensuring Regulatory Compliance
In jurisdictions worldwide, regulatory bodies like OSHA in the United States set stringent safety standards. Failure to comply can result in heavy fines, operational delays, or even shutdowns. JHA aligns directly with these requirements, helping companies document their safety practices and demonstrate compliance. For example, chemical manufacturers can use JHA to ensure adherence to protocols for handling hazardous substances, reducing both legal and safety risks. Learn how Field1st ensures OSHA Compliance for their clients.
3. Reducing Financial Costs
The financial impact of workplace incidents goes beyond immediate medical expenses. There are also costs associated with downtime, equipment repairs, increased insurance premiums, and potential litigation. A well-executed JHA significantly reduces these expenses by preventing incidents before they occur. In construction, for example, preventing a fall from scaffolding not only saves lives but also eliminates costly project delays. Discover cost-effective strategies with Field1st’s Workplace Solutions.
4. Building a Safety Culture
A robust safety culture encourages employees to actively participate in risk management. JHA fosters this mindset by involving workers in the process, giving them a sense of ownership over their safety. This collaborative approach not only reduces resistance to safety protocols but also boosts morale and productivity. See how Field1st’s Leadership Training helps instill a culture of safety within organizations.
Implementing Job Hazard Analysis: A Step-by-Step Guide
The effectiveness of JHA lies in its structured approach. While the process may vary slightly depending on the industry, the core steps remain consistent.
First, identify the tasks that require analysis. Priority should be given to jobs with a history of accidents, high-risk activities, or operations involving complex equipment. Once a task is selected, it is broken into smaller, sequential steps. For instance, welding in a fabrication shop might involve preparing materials, setting up equipment, and executing the weld.
Next, potential hazards associated with each step are identified. These hazards can be physical, such as risks of burns or cuts; chemical, such as exposure to toxic fumes; or environmental, such as inadequate lighting or extreme temperatures. For each hazard, the severity and likelihood of occurrence are assessed. This helps prioritize risks that require immediate attention.
Control measures are then developed to mitigate these risks. Depending on the nature of the hazard, controls may involve engineering changes, administrative protocols, or the use of personal protective equipment (PPE). For example, a manufacturing company might install machine guards to protect workers from moving parts or enforce strict lockout/tagout procedures during maintenance. To simplify implementation, explore Field1st’s Training and Development Programs.
Finally, all findings are documented, and the analysis is reviewed periodically. Regular updates ensure that the JHA remains relevant as tasks, equipment, or regulations change. A construction company, for instance, might revisit its JHA after introducing new scaffolding designs or safety standards.
People Also Ask
1. What is the purpose of Job Hazard Analysis?
The primary purpose of Job Hazard Analysis (JHA) is to identify potential workplace hazards associated with specific tasks and develop strategies to eliminate or control these risks. This process helps reduce accidents, protect workers, ensure regulatory compliance, and foster a safer working environment, particularly in high-risk industries like construction, manufacturing, and oil and gas.
2. Who is responsible for conducting a Job Hazard Analysis?
Supervisors, safety officers, or managers are typically responsible for overseeing Job Hazard Analysis. However, the process often involves collaboration with employees who perform the tasks being analyzed. Their firsthand knowledge of the job helps identify hazards that might otherwise be overlooked.
3. How often should a Job Hazard Analysis be reviewed?
A Job Hazard Analysis should be reviewed regularly, especially when there are changes to tasks, equipment, or workplace conditions. Routine reviews ensure that the JHA remains relevant and effective in addressing current risks. It is also good practice to revisit JHA processes after incidents or near misses to incorporate lessons learned.
4. What are the steps involved in Job Hazard Analysis?
The steps involved in Job Hazard Analysis include:
- Selecting the task to analyze.
- Breaking the task into smaller steps.
- Identifying hazards associated with each step.
- Assessing the risks of these hazards.
- Implementing control measures to reduce or eliminate risks.
- Documenting the findings and periodically reviewing the analysis.
5. How does JHA improve workplace safety?
JHA improves workplace safety by proactively identifying risks before work begins. By addressing these risks through engineering controls, administrative policies, or personal protective equipment, organizations can significantly reduce the likelihood of accidents and injuries. This not only protects workers but also ensures compliance with safety regulations.
6. Can Job Hazard Analysis prevent workplace injuries?
Yes, Job Hazard Analysis is a proven method for preventing workplace injuries. By systematically examining tasks and implementing safety measures, JHA minimizes the likelihood of hazards leading to incidents. For example, in industries like construction or oil and gas, JHA has been shown to significantly reduce accidents related to falls, equipment failure, or chemical exposure.
7. What challenges can arise when implementing Job Hazard Analysis?
Challenges in implementing JHA include:
- Lack of training for employees and supervisors.
- Resistance to adopting new processes.
- Time constraints in high-pressure work environments.
- Difficulty prioritizing tasks in large-scale operations. Overcoming these challenges requires leadership commitment, worker engagement, and a systematic approach to integrating JHA into routine safety practices.
Real-World Applications of Job Hazard Analysis
The value of JHA is best illustrated through real-world examples. In the construction industry, a company conducting JHA for roofing work identified hazards such as falls, weather-related risks, and equipment malfunctions. By implementing measures like fall-arrest systems, protective gear, and daily weather briefings, the company reduced incidents by over 50%. For practical examples, visit Field1st’s Case Studies.
Similarly, in the oil and gas sector, JHA has been instrumental in reducing pipeline maintenance risks. By analyzing tasks like valve inspections and pressure testing, companies identified potential dangers and introduced safeguards such as automated shutoff systems and specialized training for workers.
These success stories demonstrate how JHA not only prevents accidents but also enhances operational efficiency by minimizing disruptions caused by workplace incidents.
Why Job Hazard Analysis Is Essential for Workplace Safety Success
Job Hazard Analysis is more than a compliance tool—it is a proactive strategy that safeguards workers, reduces costs, and promotes operational excellence. In high-risk industries, where the stakes are especially high, JHA provides a structured framework for identifying and mitigating workplace hazards. From preventing life-threatening incidents to fostering a culture of safety, the benefits of JHA are undeniable.
For organizations seeking to enhance workplace safety, investing in a thorough JHA process is not just a regulatory requirement but a moral obligation. By prioritizing hazard analysis, businesses can protect their employees, improve productivity, and set a benchmark for safety excellence in their industry. To start enhancing your safety practices, connect with Field1st’s Experts.
Further Reading
For more information on Job Hazard Analysis and workplace safety best practices, consider exploring these authoritative resources. These links provide in-depth guidance and research to support your efforts in creating safer work environments:
- OSHA – Job Hazard Analysis The Occupational Safety and Health Administration (OSHA) offers a comprehensive guide to Job Hazard Analysis, including its importance and a detailed, step-by-step methodology for conducting effective analyses.
- NIOSH – Workplace Safety & Health Topics The National Institute for Occupational Safety and Health (NIOSH) provides valuable research-based insights into workplace hazards and strategies to mitigate risks in various industries.
- CDC – Workplace Safety and Health The Centers for Disease Control and Prevention (CDC) offers an extensive range of resources and recommendations to help organizations improve workplace safety and prevent occupational injuries.