How Digitalization Can Improve OSHA Compliance
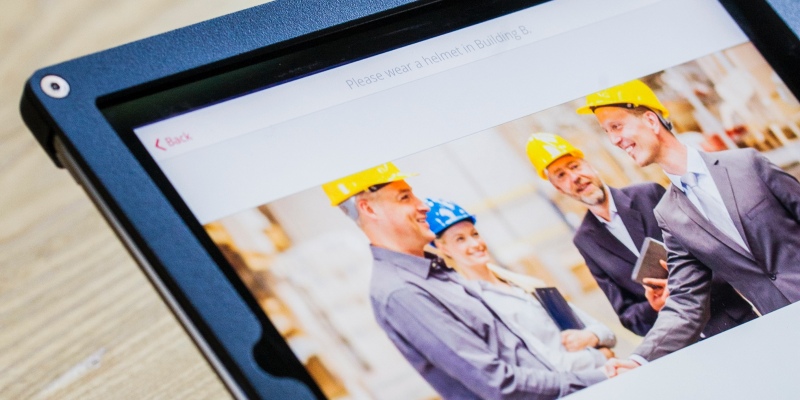
How Digitalization Can Improve OSHA Compliance
Everything is going digital with the fourth industrial revolution at hand. So, why should your OSHA compliance checking methods be any different? Safeguarding employees from dangerous situations at work should be a priority for all employers.
We can’t underestimate the importance of technology in workplaces. The same can be said for safety in workplaces. These two key factors should work hand in hand for the betterment of any industry involved. The impact the fourth industrial revolution has had on all of society is immeasurable. In turn, it has also impacted how we can meet OSHA compliance through digitalization.
In this article, we will explore the positive impact that digitalization can have on OSHA compliance.
What Is OSHA?
First, let’s gain a better understanding of OSHA with a brief overview. OSHA stands for The Occupational Safety and Health Administration. Every industry has a specific set of occupational health and safety criteria that they need to meet. Industries put these criteria in place to ensure the safety of employees while they perform their jobs.
Industries do not get to decide which parts of the criteria they wish to comply with. OSHA compliance is mandatory. Companies and organizations protect themselves and employees from unnecessary risks by ensuring that they comply with OSHA standards.
The Occupational Safety and Health Administration is responsible for ensuring compliance throughout industries. They are regulatory agents entrusted with setting standardized requirements across different industries.
All records of OSHA compliance need to be sent to their headquarters. Digitizing this process makes it much more efficient and reliable. Reports are more accurate and readily available for anyone who needs them.
The Impact Of Digitalization
There are many ways to put digital solutions in place for a company’s OSHA compliance schedule. These range from reporting and recording issues to employee and incident point tracking. You can gain more control over past and future issues by digitally recording OSHA compliance.
The use of technology throughout a company can greatly improve the speed with which it brings compliance issues to light.
Let’s explore some ways digitalization can improve a company’s compliance.
1. Accurate, real-time reporting
The implementation of digital record keeping has many benefits. You can update issues and pull up any history in real-time. This is an extremely powerful tool that allows a company to better track and manage potential risk areas.
You don’t have to create your own digital records: there are numerous software options available that do this for you. One of the easiest ways to record information is to create checklists and notes. You can upload these for sharing through cloud services. With a mobile safety app, you can update information in real-time, and it will be accessible to the individuals that need them in real-time.
Digital access to previous and current OSHA compliance checklists helps when being audited. This is because you have easy access to crucial information. In addition, you can track areas of your operations that are not compliant.
You can also track the actions you took to rectify previous compliance issues. Outdated paper checklists and documents are more likely to get lost than digital ones.
All these records are great tools during your compliance audits. Efficient reporting and record-keeping mean you know what has been done and what still needs to be done. While being audited, companies can provide proof of the steps they took to fix previous problem areas.
2. Handheld technology
Technology has come a long way in the last decade. There are many tools that you can use to improve safety standards across your organization and operations. If you implement these correctly, you can drastically reduce the risk for your workers both in the workplace and out in the field. Some of the tools that you can use are a lot simpler than you might think.
For example, smartphones are one of the most readily available tools out there. Everyone has one. These can greatly improve tracking and reporting and make safety resources and instructions readily available to your workers. Managers can use smartphones for real-time reporting and monitoring progress through apps.
You can even equip them with emergency features like panic buttons. This way, you can know immediately should there be a critical event. Being able to report these events almost instantly reduces the chance of further complications. In addition, it enables emergency services to be contacted or other appropriate action to be taken without delay through geolocation features.
Common Compliance Issues Solved through Digitalization
There are many compliance issues companies may face. However, some are more prevalent than others. Through the correct implementation of a digital solution, companies can mitigate these risks.
Fall Protection
Fall protection is the most common compliance area in which companies are non-compliant. A fall from any height can have serious consequences for an employee and the employer.
Most fall protection or fall prevention systems are not digital. However, you can digitize identification and record keeping. This can greatly improve safety for all employees. One of the easiest ways to improve fall protection compliance is through staff training on safety protocols.
Hazard Communication
Most companies in the utilities or industrial sector face certain hazards. For example, if they store chemicals on-site, they need to ensure that they are identified and stored properly. It’s also important to keep an accurate record of them.
Digitization of documents and communication makes it easy for companies to track, document, and share the details of all hazardous materials they deal with. This ensures that everyone is in the know about what they store on site.
With a safety app, you can also ensure that all workers and stakeholders have access to resources on how to handle hazardous materials or situations. Should there be any issue, workers can easily look up how best to deal with the situation. Having this type of safety management system in place is crucial for risk management.
A digital solution also ensures that all relevant parties have access to real-time updates should an incident occur. This way, they can deal with incidents immediately and resolve them before they get any worse. This is incredibly important when dealing with any environmental hazard.
Respiratory, Eye and Face Protection
Companies that deal with any potentially hazardous materials also require personal protective equipment (PPE). This includes respiratory devices, as well as eye and face protection. It’s important to keep protective equipment at an adequate stock level and in good working condition.
PPE compliance becomes easy through the effective use of digital systems that track and report on these items. A digital solution can help managers to train their workers on when they need to wear protective equipment and why. This can help them enforce better workplace health and safety practices to comply with OSHA.
Conclusion
As we can see, there are many ways that digitalization can help make OSHA compliance easier. Companies can greatly improve working circumstances for all employees by embracing the technological advancements available.
The goal at the end of the day should be to improve the overall safety of employees. In addition, you want to reduce the risk of incidents for the employer. These are not mutually exclusive. By improving one, we can improve the other.
OSHA compliance will become a digital process in the future. By embracing the options available to you now, you will avoid any issues later on. So, be sure to check out Field1st and see how it can help you maintain and improve compliance.