The Key To A Successful Safety Program for Your Workers
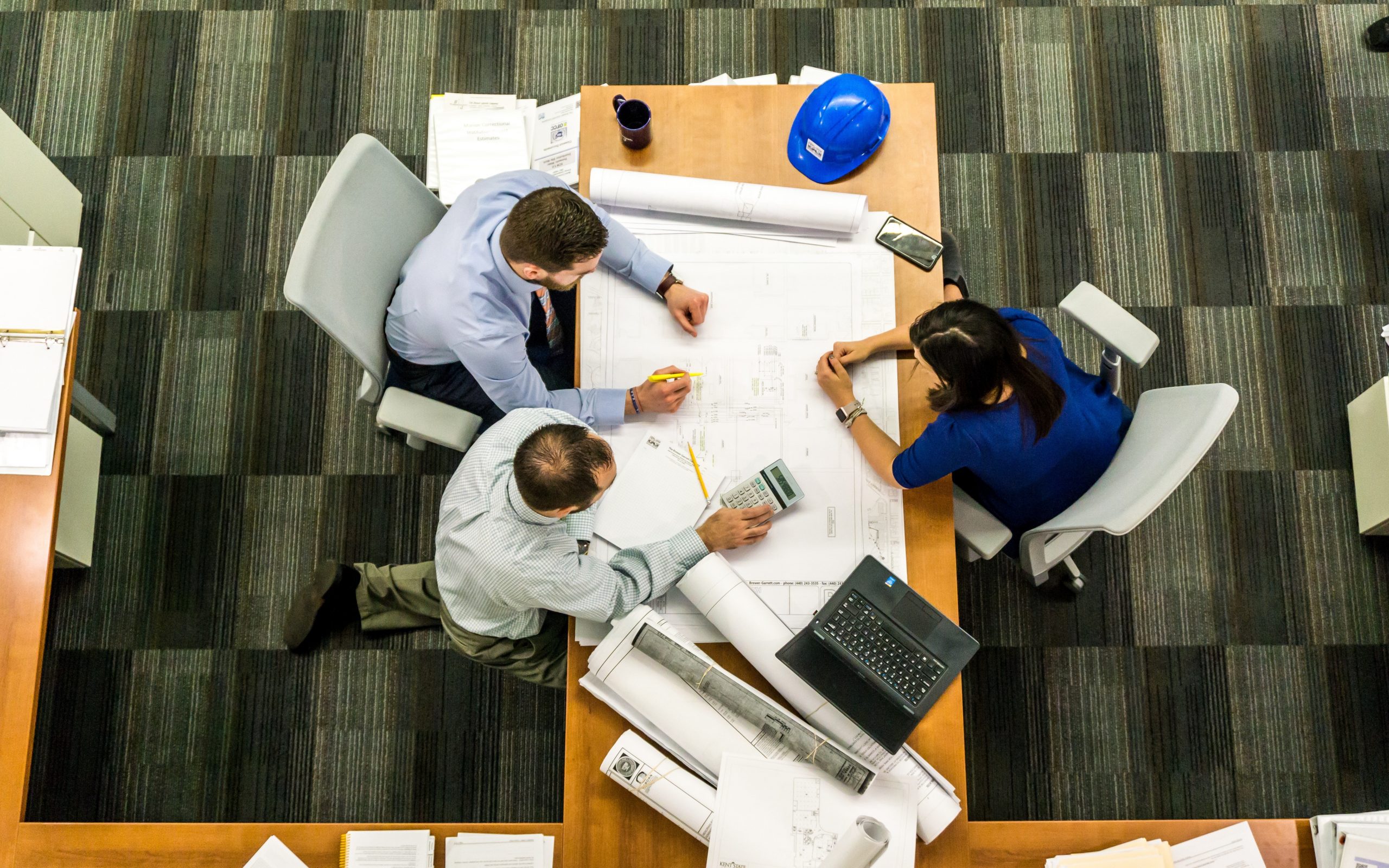
How to Implement a Successful Safety Program for Your Workers
No matter the industry or the workplace’s size, having a clear safety program in place is essential. Workplace safety always needs to be a priority for employers. It helps keep workers safe, protect the business’s financial assets, and comply with necessary safety standards.
It’s important that employers or managers introduce workplace safety as a program and not just a project. A successful safety program will help to reduce the risk of any incidents in dangerous work environments. And, it will make sure that the company covers all its bases in terms of safety standards.
What is a Safety Program?
A safety program offers clear guidelines and protocols based on workplace safety. This program needs to be specific to each work environment. Creating an industry-specific set of safety protocols reduces the risk of any workplace incidents and accidents. Not only this, but it helps to keep your business in line with the safety standards you must comply with by law.
These programs clearly lay out the risks of a workplace and checklists that all workers follow to avoid incidents. This can cover a wide range of procedures, and it’s important to create it in line with OSHA safety standards.
Having a safety program like this provides a long-lasting system for keeping workers safe. And it eliminates dangerous or risky practices.
When developing a strong safety program, it’s good to involve workers from various areas or departments. By doing so, you can address everyone’s concerns.
Overall, these programs help to hold businesses accountable for safety procedures. At the same time, they help to create a safer workplace by mitigating hazards.
Creating a Successful Safety Program
Keep your employees safe and your business covered by creating a comprehensive program. Here are some of the key steps toward developing and implementing new strategies around safety.
Make Safety a Clear Priority
To spread awareness around safety, your company needs to communicate its importance as a key value. You need to prioritize safety within the business, including its importance in the company’s mission statement.
It would be best to implement safety descriptions into different roles in the business with clear safety objectives.
For implementing a successful program on safety, safety must be first recognized as an essential commitment within the company. This needs to be communicated company-wide. As such, it’s essential to make safety policies and standards easily visible and accessible.
When demonstrating your business’s commitment towards safety, you need to roll out proper investigations of any incidents and dangerous work sites. This shows your workers that you take their safety seriously.
The Safety Role of Management
It is important that staff and management work together when implementing a new program. Management needs to prioritize safety procedures (as mentioned above) by creating the plans and designing the program around safety. It is their job to implement the guidelines and protocols.
However, a good program requires input from all sides. Employees need to work alongside management to follow through on the procedures they put in place.
Employees must add input to new safety systems and provide feedback to systems in place.
Risk and Hazard Assessment
Conducting thorough assessments of the workplace and all its risks is a key requirement before developing a safety program. This should include an in-depth investigation of all worksites and a look into any employees’ safety concerns.
The insight from employees in these workspaces is incredibly valuable as they deal with the risks daily. Risk identification and hazard assessment are critical processes in making a workplace safer.
When performing a risk assessment, it’s best to categorize the different hazards present. This includes workplace hazards, environmental hazards, and activity hazards. Without first clearly identifying these hazards, you won’t be able to put an effective safety program in place.
Control and Prevention
In the best-case scenario, you can prevent safety hazards altogether. Once you identify problems, you can put procedures in place to remove that risk completely. However, there are some work hazards that you cannot avoid. But, rather, they require a high level of control.
Hazard elimination and hazard reduction processes are different things. Safety officers need to employ both wherever applicable. In hazard reduction practices, it’s important to conduct regular monitoring and evaluation of the processes. This will help you to keep an eye on it over time.
Create Clear Safety Guidelines
Now that you understand workplace hazards, you will need to start laying out clear safety guidelines. The only way to really hold organizations accountable for their employees’ safety is to have the necessary guidelines clearly written out.
This should include outlining the risks and potential hazards associated with each work area. It should also include the job functions and specific safety requirements for each employee.
Clear and concise safety guidelines are critical for an effective safety strategy. It ensures that employees understand what is required so that no misunderstandings occur.
Training
Once you identify all safety hazards and establish clear protocols, it’s time to get all employees on board. No matter how good your safety protocols and guidelines are, they mean nothing if you do not implement them properly through training.
It’s, therefore, crucial to put proper training procedures in place. This will ensure that all employees become well-informed about the safety procedures in place.
Everyone in the workplace needs to be made aware of the risks involved. They also need to understand exactly what to do in the event of incidents and accidents.
Training should be an ongoing process, with refresher courses happening regularly. After all, a safety procedure is only effective if employees follow through with it after proper training.
Investigation and Evaluation
A program should never just be created and implemented once off. It should be a consistent procedure that is constantly under evaluation.
One of the first things to do when implementing these programs is to investigate past accidents. This will help you find their causes to put measures in place to prevent the same event from happening again.
By doing this, you can eliminate the chance of the same accident happening twice. To make sure this is working, safety managers should continue to go back to their past investigations and evaluate how the safety guidelines are working overtime.
Even with a thorough safety process in place, there is still room for new hazards to present themselves. As such, safety inspections should be a regular process. Safety managers should always be open to finding and resolving new workplace hazards.
Employee feedback should also be a continuous process. It is important to understand what people experience daily and how effective the safety guidelines are.
Final Thoughts
All employers need to take safety seriously in the workplace. Eliminating the risk of incidents is necessary for a more productive workspace and one that meets all necessary safety standards.
By having a proper safety program in place, employers will eliminate legal challenges and protect their workforce and assets.
A safe work environment is critical for any industry, and this is only possible with a successful program in place. Using industry-tailored safety software and technology can help to optimize this process. It can make managing safety much easier and more effective!